7 Millionen Tonnen Ölschiefer „schlummern” noch im Bächental, sagen Geologen. Eine schier unglaubliche Menge. Da aber ein Großteil des Schiefers tief unter der Erde liegt und nur oberirdisch abgebaut werden kann, ist man bestrebt, mit dem wertvollen Rohstoff schonend umzugehen, damit auch die nächste Generation das Werk ihrer Väter zum Wohle der vielen Kunden fortführen kann.
Seit 1994 ersetzt im Bächental nach und nach die Technik die schwere Handarbeit. Etwa alle drei Wochen werden während der Brennsaison, die von Juli bis Oktober dauert, sechs bis acht etwa drei Meter tiefe Löcher mit dem handgeführten Pressluftbohrer – im Tagebau – in den Fels gebohrt. Diese werden mit genau dosiertem Sprengstoff gefüllt, der elektrisch gezündet wird. Da der Ölschiefer im Tagebau gewonnen wird, muss zuvor das etwa einen Meter über der Ölschieferader liegende Erdreich – Streichrichtung von Ost nach West, 70 % Fallrichtung nach Norden – abgetragen werden. Die Mächtigkeit dieser Gesteinsader beträgt 6 bis 8 Meter und ist in die Hangenden und Liegenden“ des Liaskalks eingekeilt. Der Ölgehalt des Schiefers beträgt 3 bis 6 %.
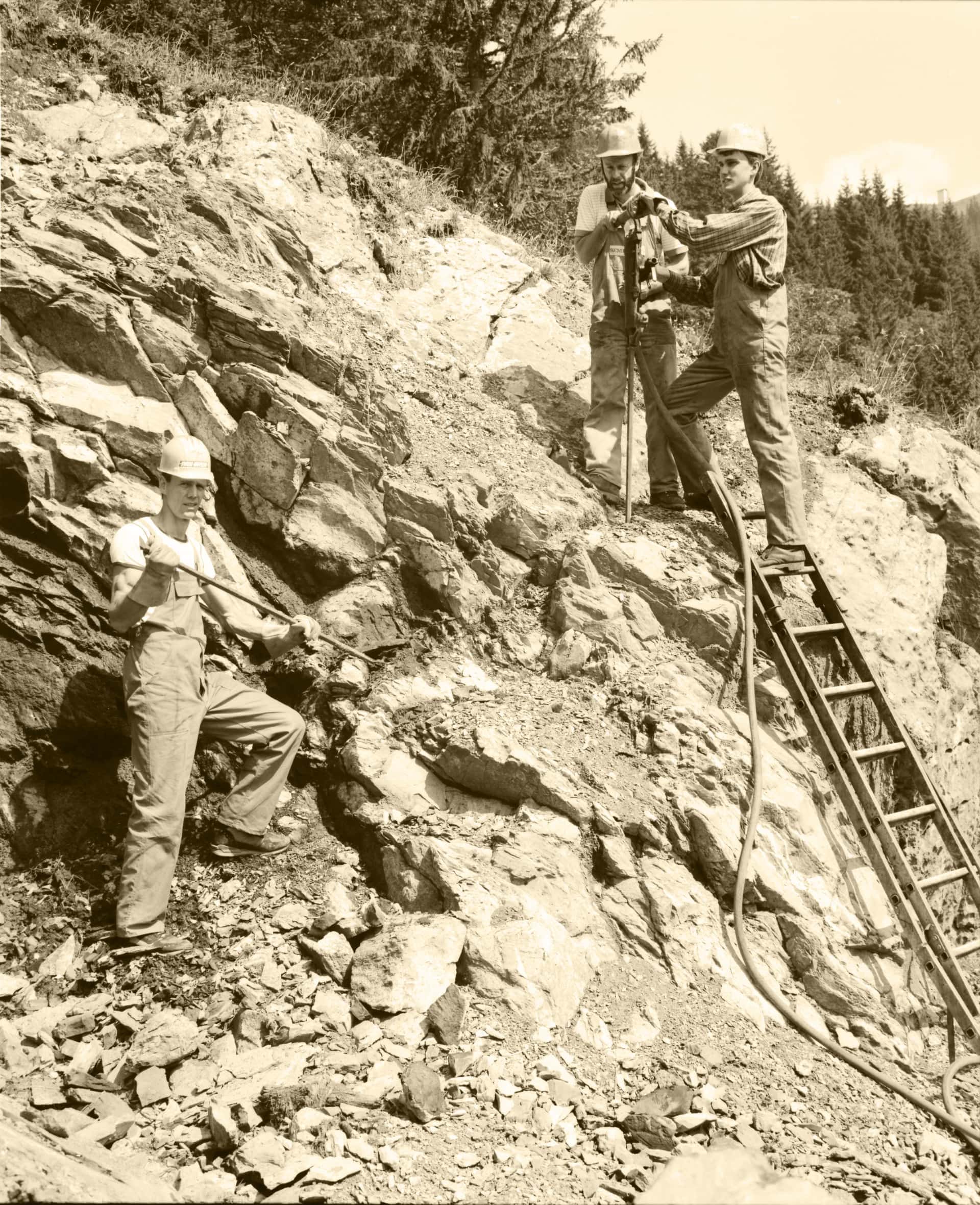
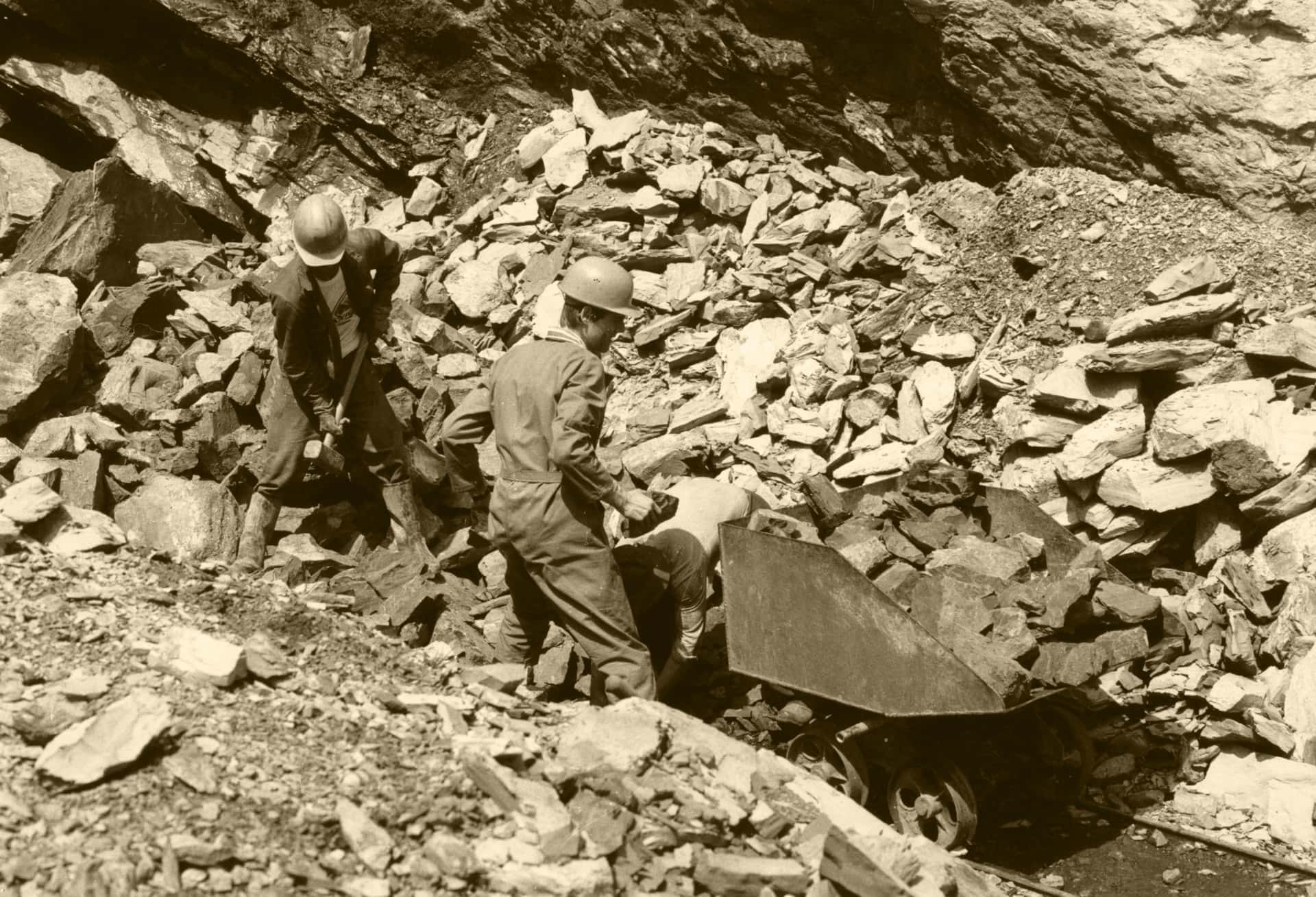
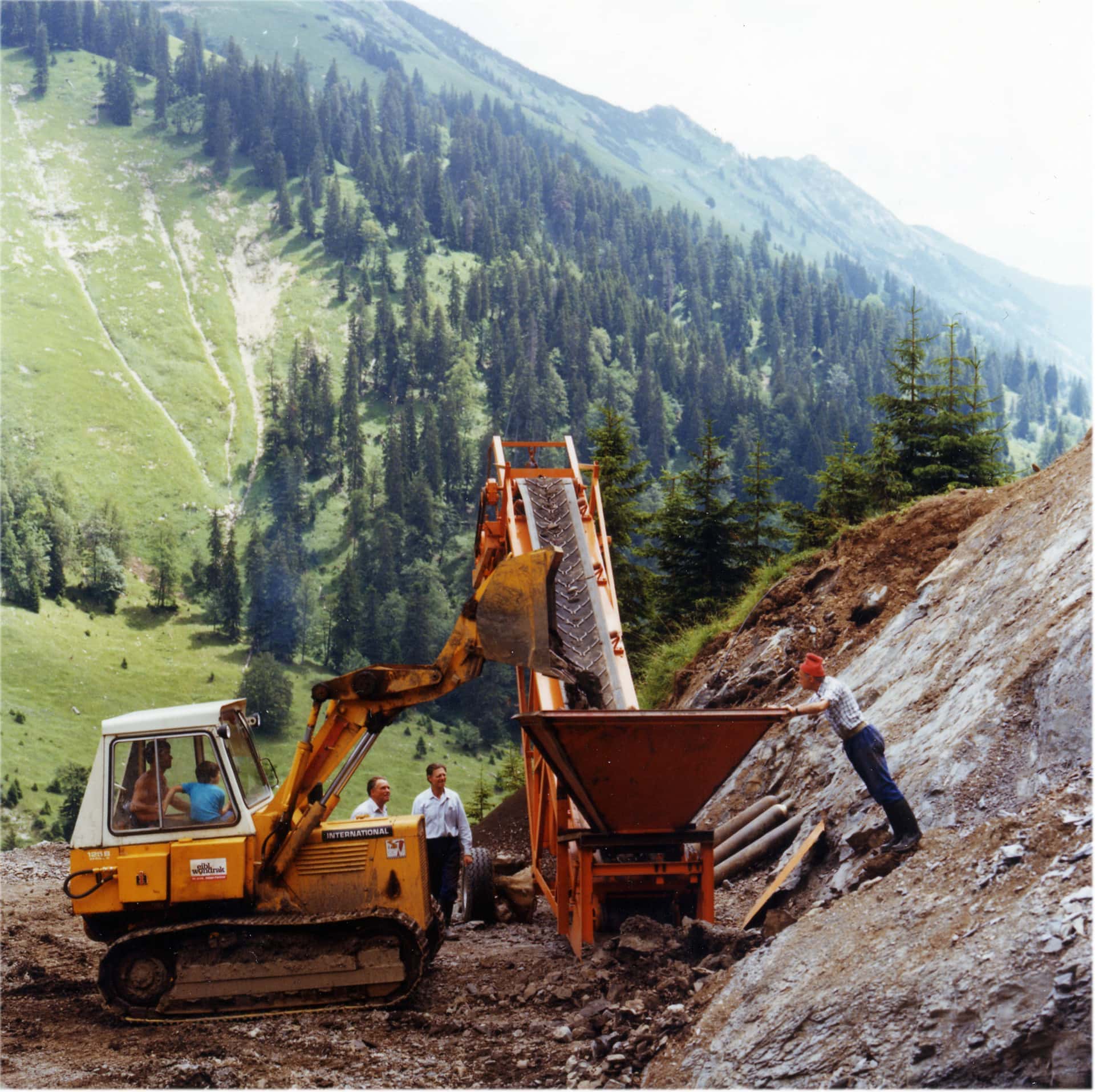
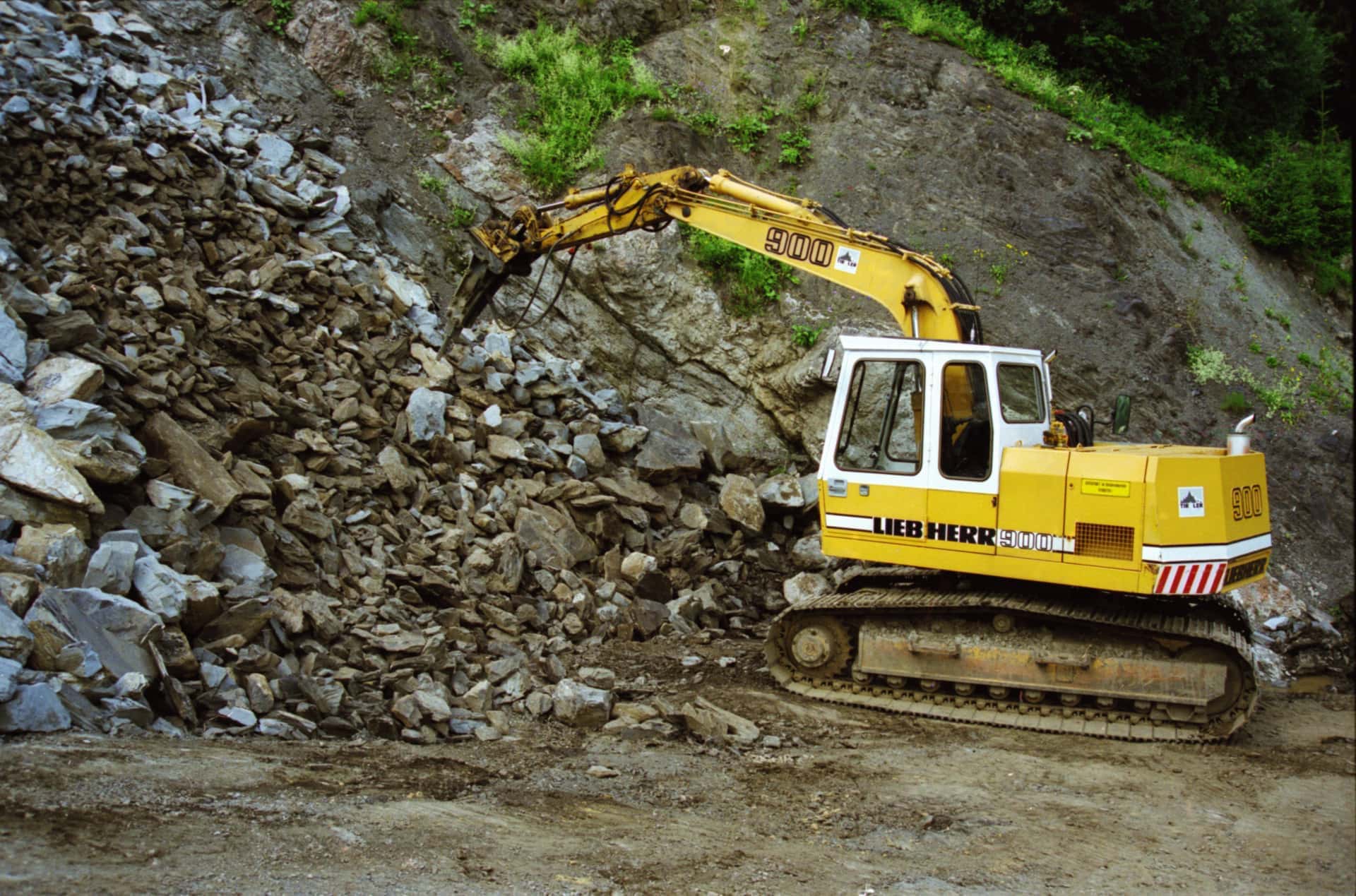
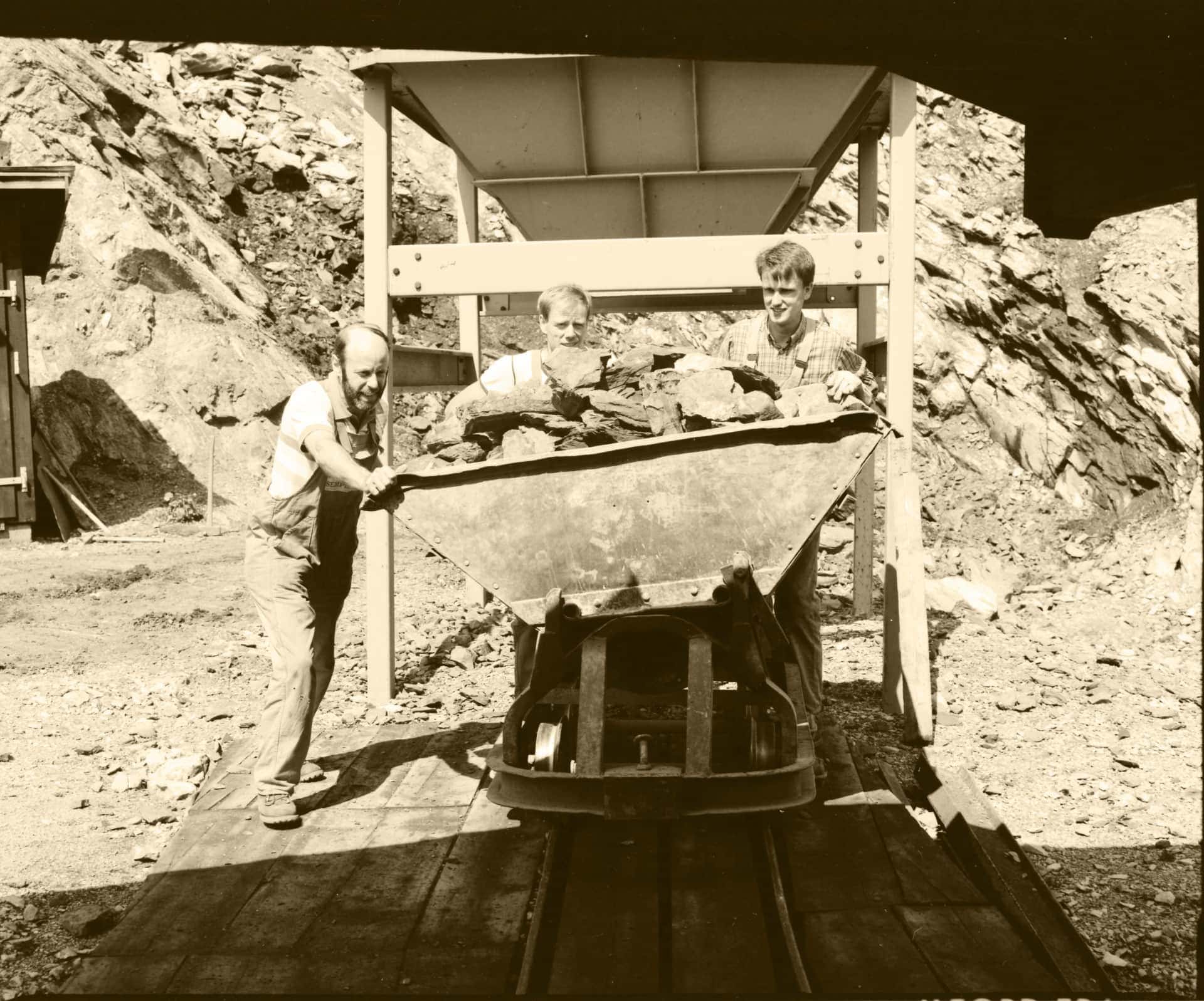
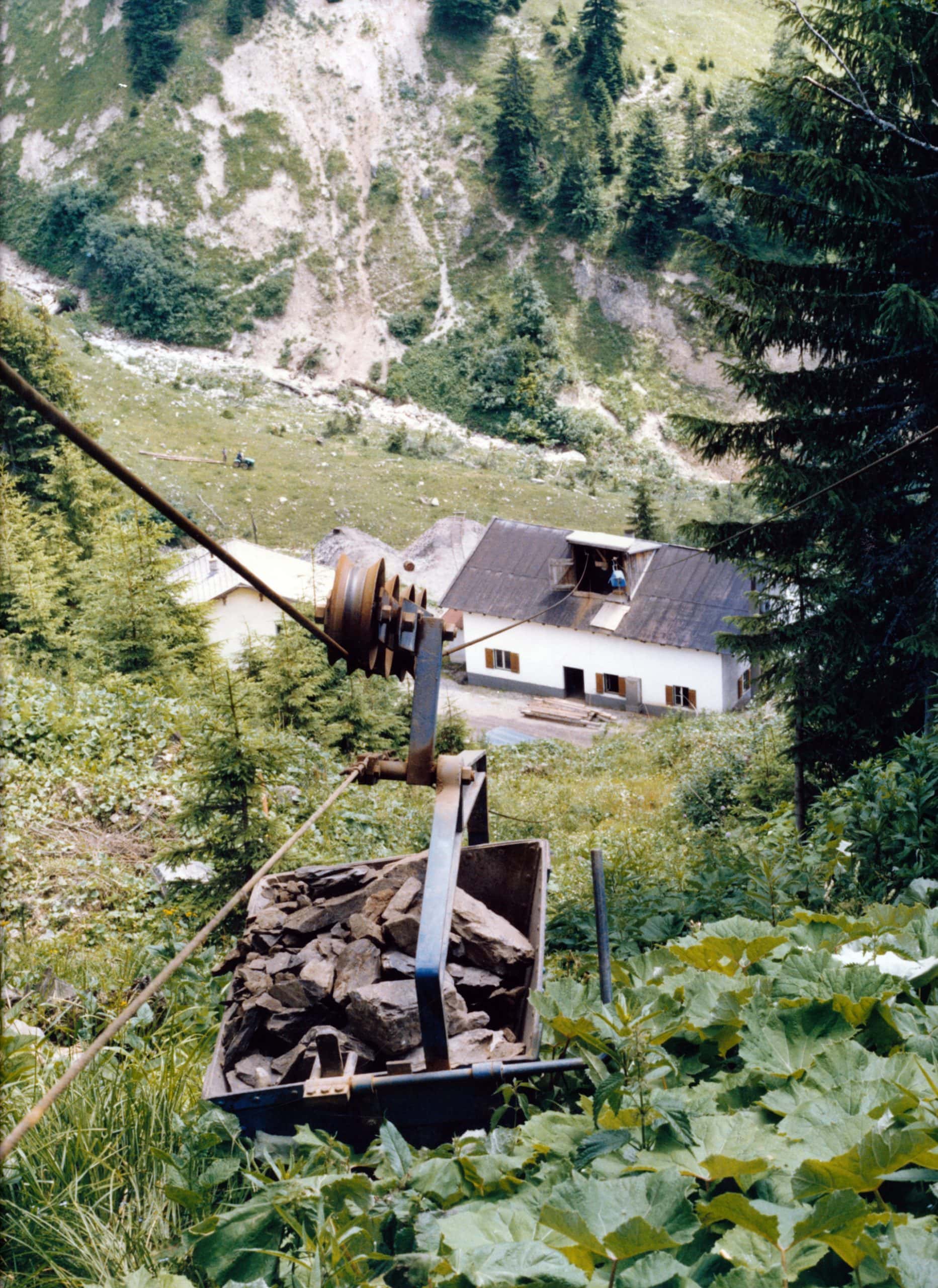
Nach der Absprengung kommt der Raupenbagger zum Einsatz, dessen anflanschbarer Hydraulikmeißel beim Zerkleinern des „Haufwerks“ auf Kopfgröße mehrere Arbeiter ersetzt. Anschließend wird das Rohmaterial, von dem täglich etwa sieben Tonnen gewonnen werden, mit einem Radlader zu einer Siebanlage befördert. Dort erfolgt die Klassierung, die Trennung von Erde und Schiefer. Mit einem Grubenhunt wird der vorgereinigte Ölschiefer dann zur Bergstation der Materialseilbahn transportiert, die den Ölschiefer ohne Energie, nur mit Hilfe der Schwerkraft, im sogenannten „Bremsberg“-Verfahren in einer Mulde über ein 190 m langes Tragseil zur 100 m tiefer gelegenen Schwelanlage befördert. Dort angekommen, wird der Ölschiefer direkt vor die Öffnung des Backenbrechers gekippt, der die Steine nochmals auf Faustgröße zerkleinert. Ein Rüttelsieb entfernt die für den Schwelprozess ungeeigneten Feinanteile, da diese die Strömung der Schwelgase behindern würden. Über ein Förderband gelangen die „Zehnersteine“ zu den Schachtöfen. Die Arbeiter entnehmen das Schwelgut nicht mehr wie früher von Hand mit einer Gabel, sondern mit einem Minibagger und „füttern“ damit die gefräßigen Mäuler der viereinhalb Meter hohen, mit Schamottesteinen ausgekleideten Schachtöfen. Das geschieht 16 Mal in 24 Stunden. Sieben Tonnen Ölschiefer werden in den drei Sommermonaten täglich im 90-Minuten-Takt in die drei Schachtöfen gefüllt, um daraus rund 120 Liter TIROLER STEINÖL zu gewinnen. Nach der bereits im Blogbeitrag „Vom Stoan zum Öl“ beschriebenen Schwelung bzw. Trockendestillation und Kondensation im 120 m langen Röhrensystem ist das Steinöl für die weitere Verarbeitung bereit.
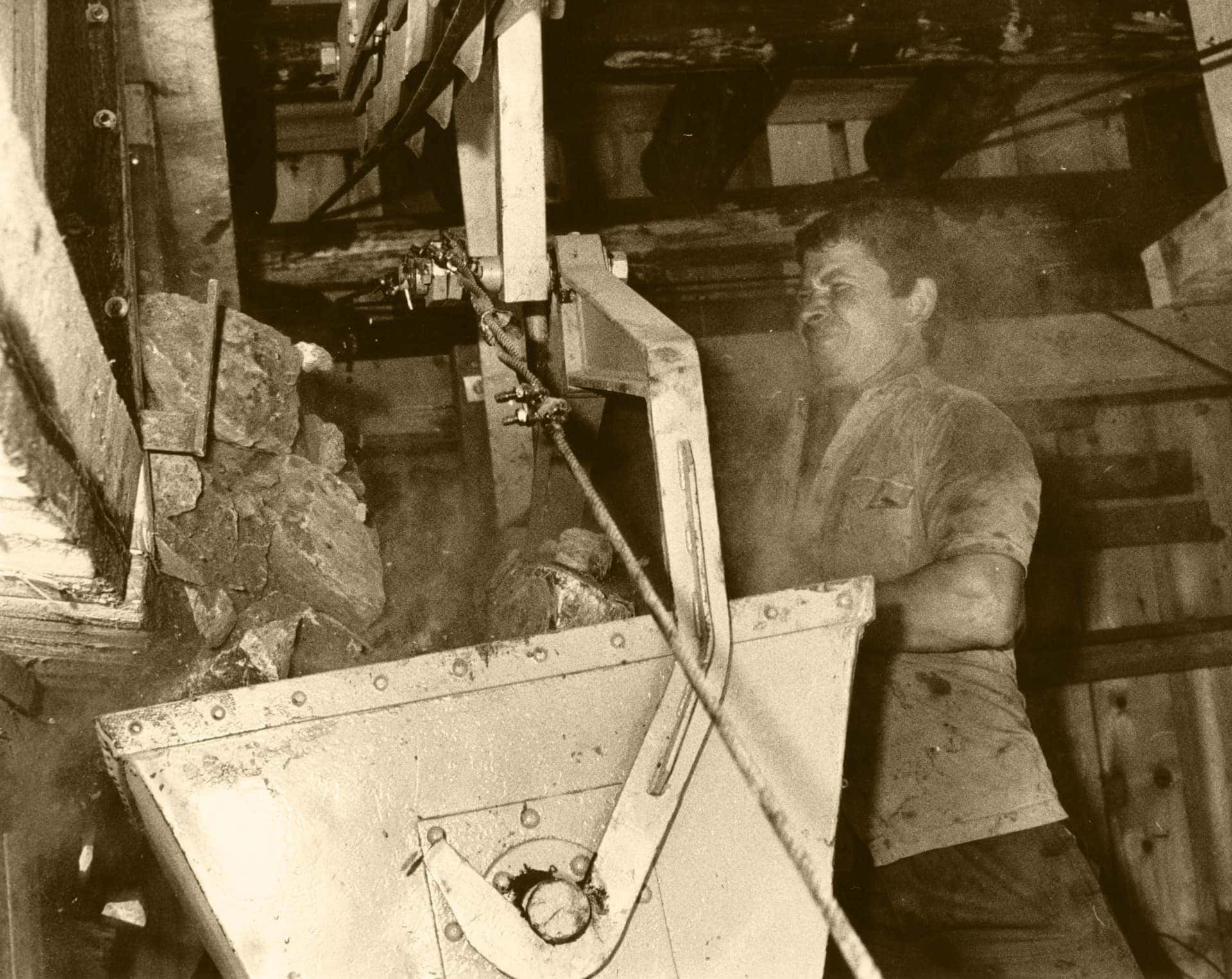
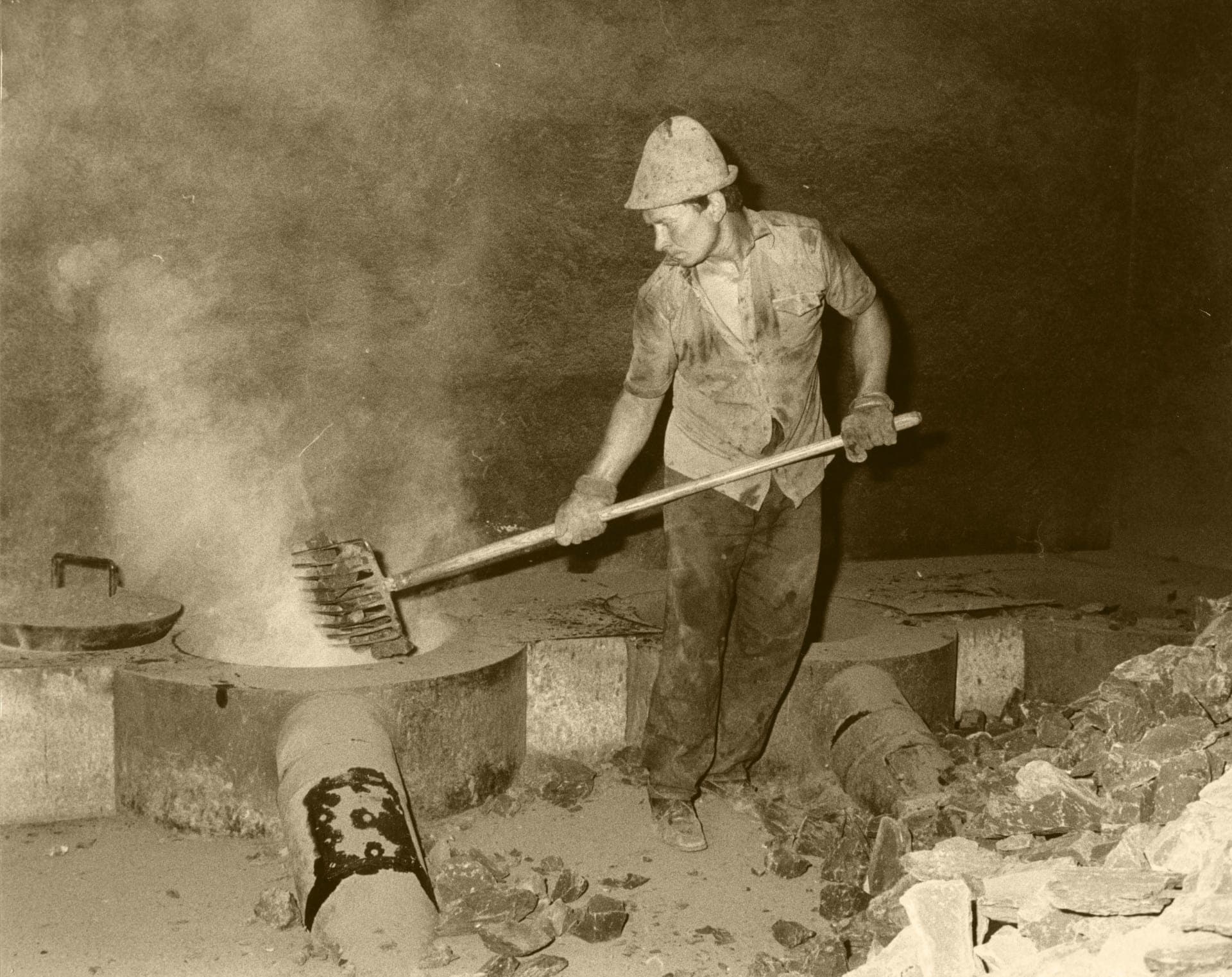
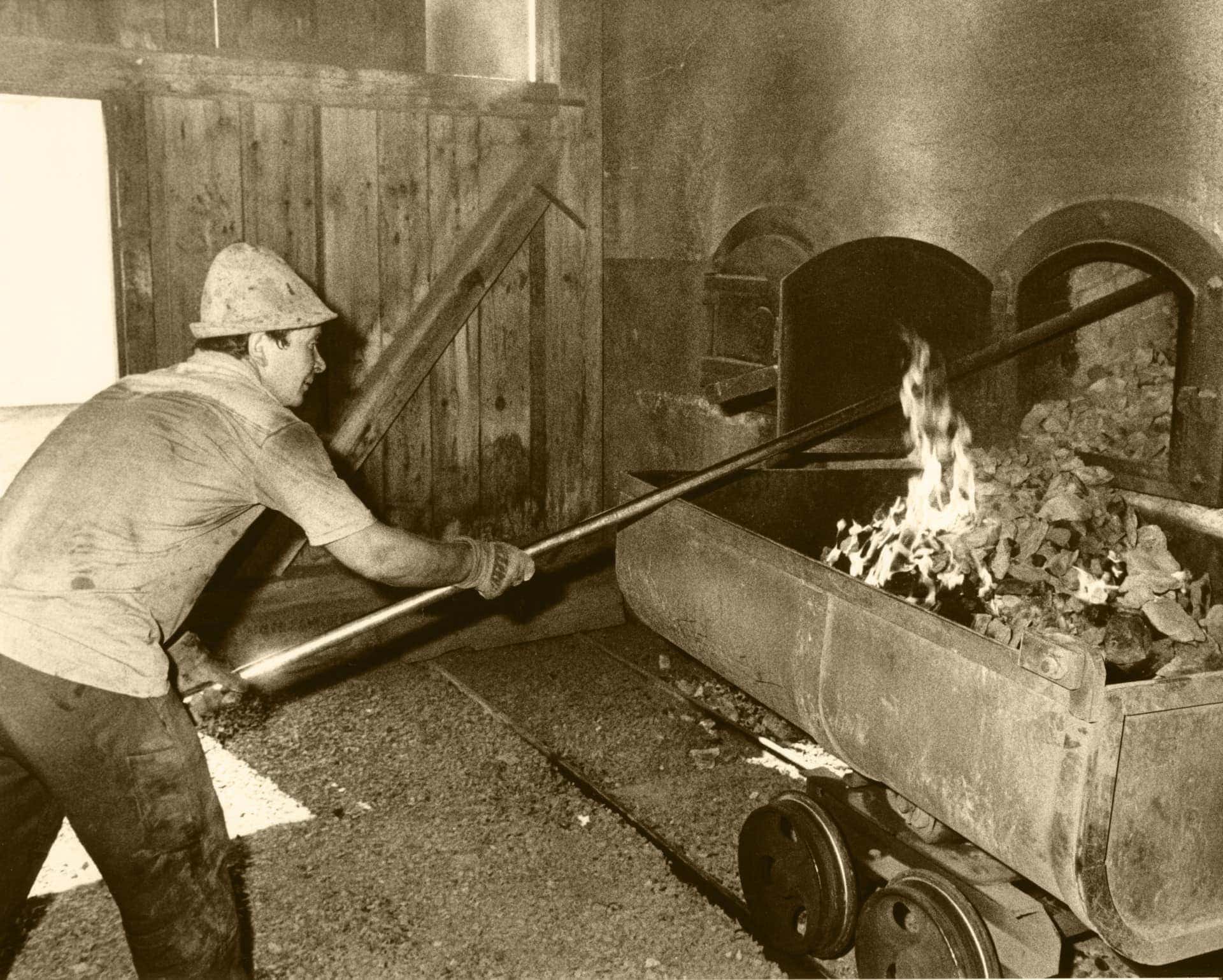
Dieses Verfahren wurde bis 2006 angewandt, seither wird das TIROLER STEINÖL in einem modernen, computergesteuerten Schwelofen gewonnen (siehe dazu die Blogbeiträge: Die neue Schwelanlage Teil 1 und Teil 2). Die Gewinnung des Ölschiefers im Tagebau, der Transport mit der Materialseilbahn sowie die händische Zuführung des Ölschiefers zum Backenbrecher sind jedoch nach wie vor die gleichen Arbeitsschritte.
Nach der anschließenden Reinigung wird das TIROLER STEINÖL im Veredelungsbetrieb in Jenbach zum Wirkstoff für alle Steinöl-Produkte weiterverarbeitet. Diese werden im werkseigenen Labor einer strengen Qualitätskontrolle unterzogen. Die Abfüllung in Flaschen, Tuben und Dosen erfolgt ebenfalls im Werk Jenbach, während Etikettierung, Lagerung, Verpackung und Versand im Hauptsitz der TIROLER STEINÖLWERKE in Pertisau erfolgen.
